Modern welding solutions - money found out of thin air
In terms of air quality control in industrial production, the issue of welding fume extraction has become more important over the years. Welders and other employees in the production area are exposed to a variety of hazardous volatile particles that can cause permanent health damage, even cancer: The 2019 Occupational and Environmental Health Cohort Study, which involved over 17 million welders from Germany to the US, clearly demonstrated that people exposed to welding fumes - and welders in particular - are 43% more likely to develop lung cancer.

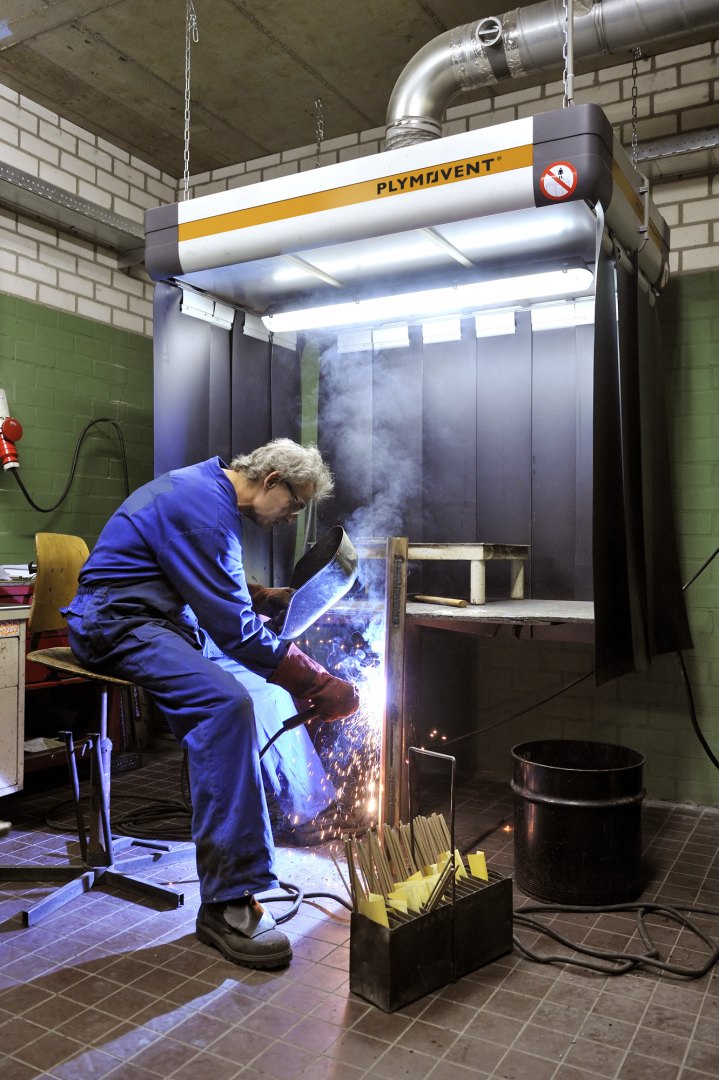
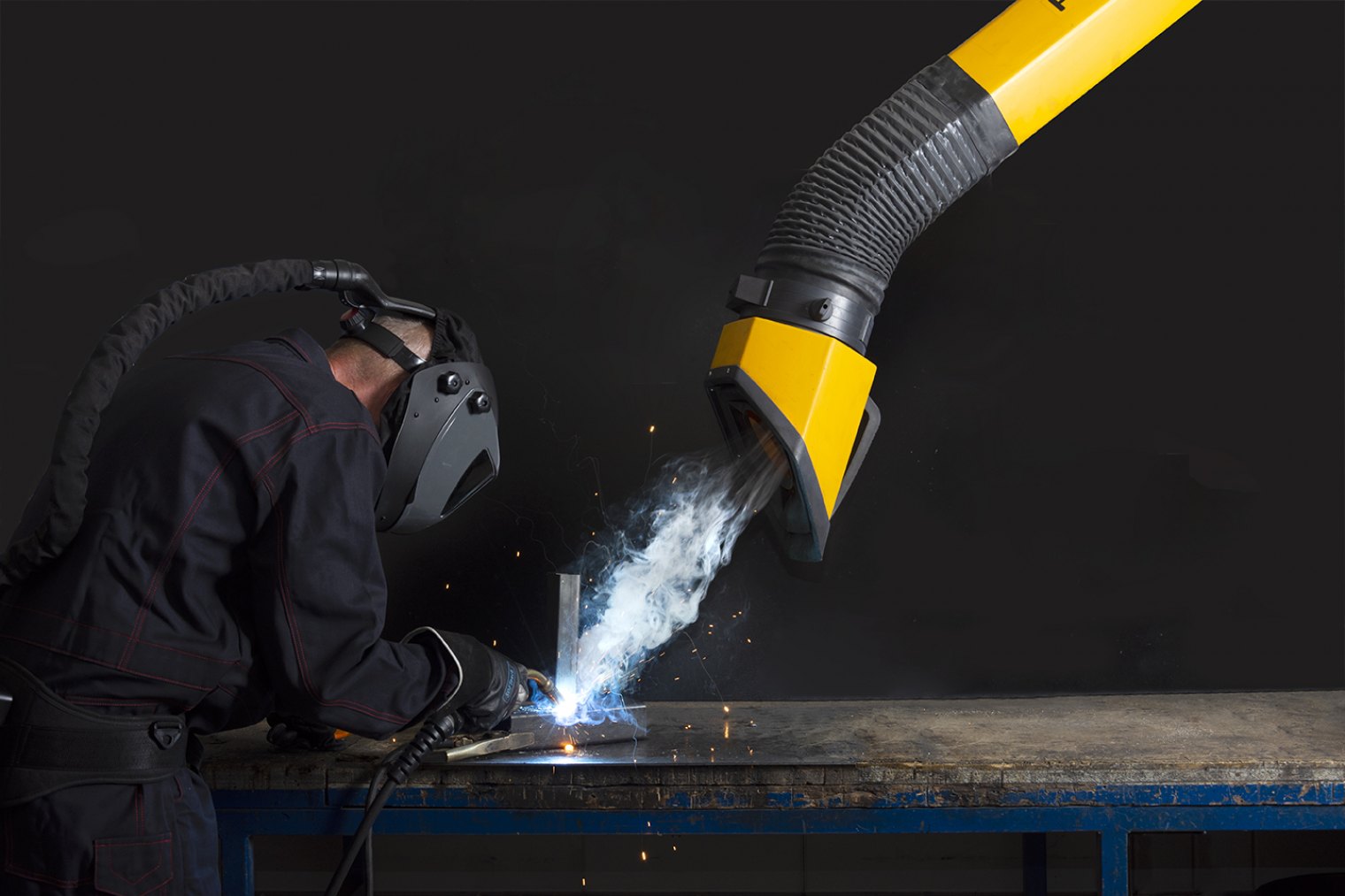
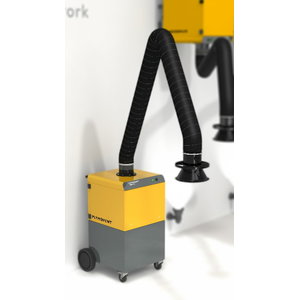
Mobile welding fume extractor MobileGo, 3m Economy arm, Plymovent
SALE
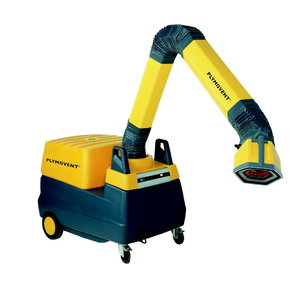
Mobile welding fume extractor MFD 435 (without arm), Plymovent
SALE
Unleashing Performance in the Motorsport Industry | Milwaukee Tools for Time-Critical Demands
Join us as we travel to major tracks across the globe, where tools and solutions must never fail. From impact wrenches to drills, and grease guns, MILWAUKEE® outperform the competition, providing strength and productivity to accomplish more in less time. But MILWAUKEE® is more than just power tools; it is a comprehensive brand offering a wide range of hand tools, toolboxes, and personal protective equipment (PPE) to meet all your needs. Experience why professionals proudly rely on MILWAUKEE® to get the job done every single time in the fast-paced motorsport industry. MILWAUKEE® Transport Trade Tools: https://www.milwaukeetool.eu/en-eu/trades/transport/ Milwaukee Tool Website: https://www.milwaukeetool.eu/ Store Locator: https://www.milwaukeetool.eu/support/store-locator/ #milwaukeetools #tradesman #transport #aerospace #automotive #railway #marine
MILWAUKEE® M18™ Cordless System
The MILWAUKEE® M18™ cordless system represents the ultimate synergy of professional-grade power, lightweight, extreme performance and superior ergonomics. Powered by REDLITHIUM™ battery technology for unmatched run-time, and coupled with patented technologies, innovative motors and advanced electronics, M18™ changes the game. Focused on improving productivity for professionals in the trades, MILWAUKEE® offers more than 215 performance-driven solutions that are fully compatible with the M18™ family — the fastest-growing 18V cordless system on the market. More on the M18™ system: https://www.milwaukeetool.eu/systems/m18/ Milwaukee Tool Website: https://www.milwaukeetool.eu/ Store Locator: https://www.milwaukeetool.eu/support/store-locator/ #MilwaukeeTools #MilwuakeeToolEU #M18
MILWAUKEE® M12™ Cordless System
MILWAUKEE® Job Site Solutions
.jpg)
Stokker Expands in Finland
On January 2 Stokker OY successfully concluded a deal to acquire Mateko Invest OY in Finland. Mateko Invest owns the businesses Mateko OY, the JCB construction machinery dealer in Finland, and CE Rental OY, specializing in renting JCB machines.
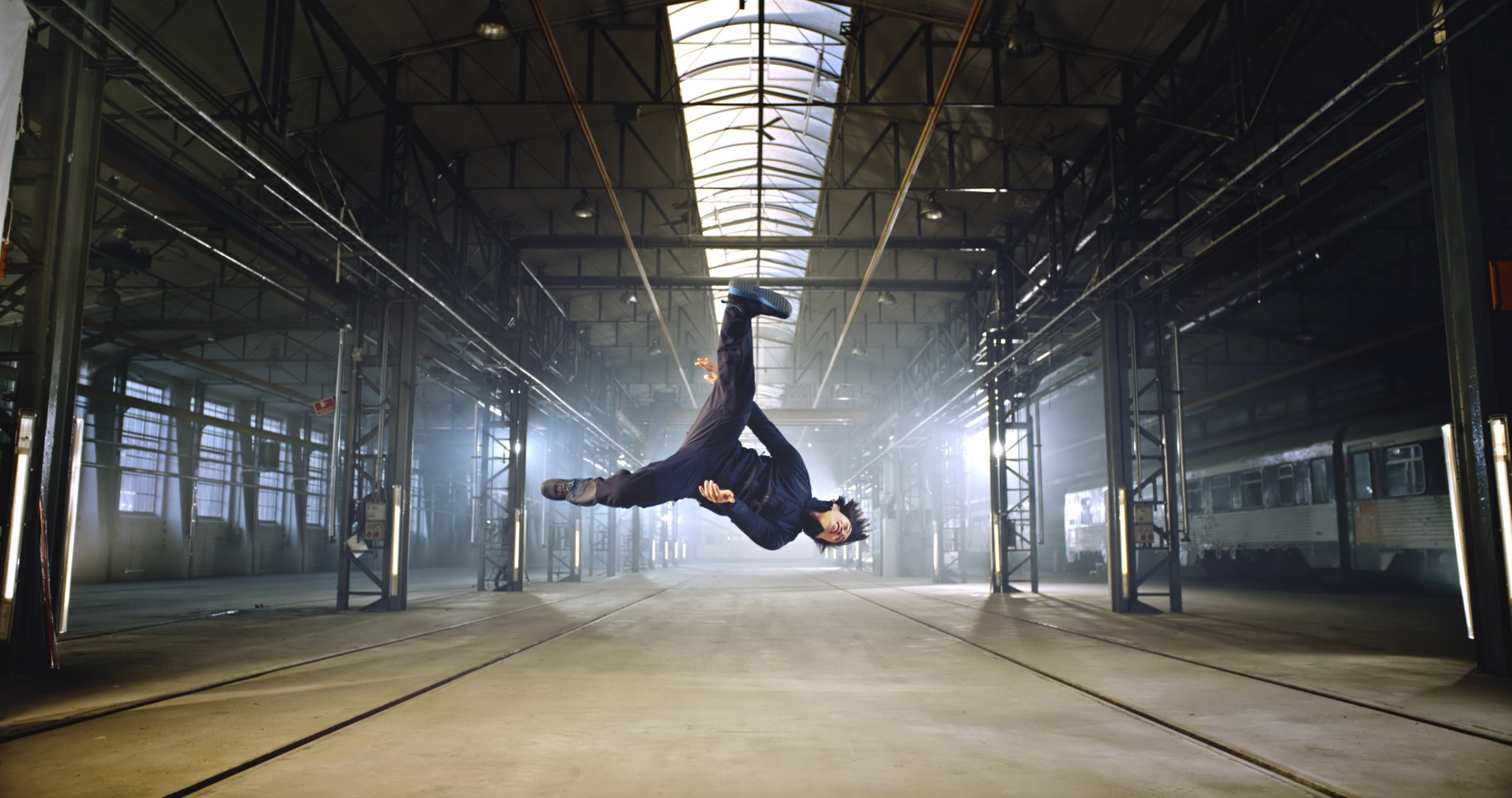
Selecting work trousers
The best work trousers are comfortable, have a good fit, are functional and durable, but also have a modern and pleasant design.
At construction works, trousers are not merely pieces of clothing that provide safety, but also help you keep warm and temporarily attach tools when working outdoors. It is important that the trousers are waterproof and breathable when working outdoors, especially in the Estonian climate.
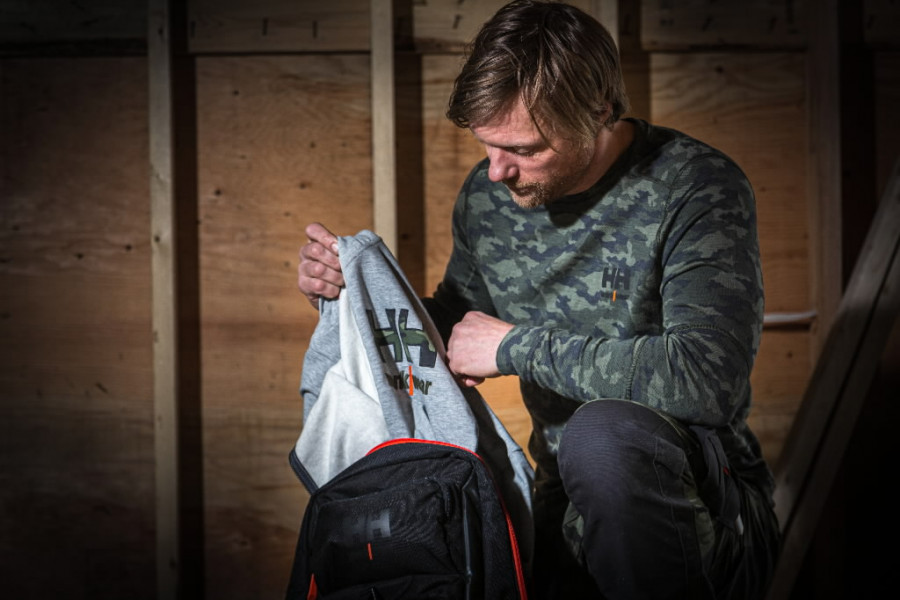
Selecting warm underwear. Which warm underwear is the best?
Warm underwear, thermal underwear, underwear, work underwear… There are a lot of names.

How To Choose And Keep Sixton Peak Footware in Perfect Shape?
Buying an excellent safety shoe is not enough, you have to take care of it, clean it and replace the components subject to wear (with the accessories provided by Sixton Peak®). In this way it is possible to preserve over time not only the characteristics of comfort and protection but also the PPE certifications.